What is SS316 Cathode Plate Laser Welding?
SS316 Cathode plate laser welding involves using a focused laser beam to join metal plates, creating strong and precise welds. It’s commonly used in industries like electronics and battery production, where accuracy and durability are critical.
Benefits of SS316 Cathode Plate Laser Welding
- High Productivity: Laser welding is fast and efficient, boosting production rates.
- Strong Welds: The concentrated heat of the laser ensures deep penetration, creating robust, durable welds.
- Smooth Surface: Laser welding minimizes distortion and results in a clean, smooth finish.
Step-by-Step Process of SS316 Cathode Plate Laser Welding
1. Pick Up the Blade
Start by picking up the welding blade, which holds the cathode plate in place during the welding process.
2. Position the Blade Correctly
Place the blade in the right position to ensure the cathode plate is securely aligned with the laser welding machine.
3. Pick Up the Conductive Beam
Now, pick up the conductive beam, which transmits the laser energy to the welding point.
4. Align the Beam and Adjust the Blade Angle
Position the laser beam at the correct angle and adjust the blade to ensure optimal alignment for a precise weld.
5. Start the Laser Welding
Activate the laser, and the heat will fuse the metal plates, creating a strong, clean weld.
6. Pick Up and Place the Welded Cathode Plate
Once welding is complete, carefully pick up the welded cathode plate and place it on a rack to cool.
Why Choose SS316 Cathode Plate Laser Welding?
- Precision: Laser welding offers exceptional precision, resulting in clean and aesthetically pleasing welds with minimal distortion.
- Heat Control: The localized heat input reduces the risk of warping and allows for the welding of thin materials.
- Automation: Laser welding systems can be easily integrated into automated production lines, enhancing efficiency and consistency.
- Quality: The weld quality is typically superior, with higher strength and fewer defects.
Applications
Laser welding of stainless steel plate

Laser welding process
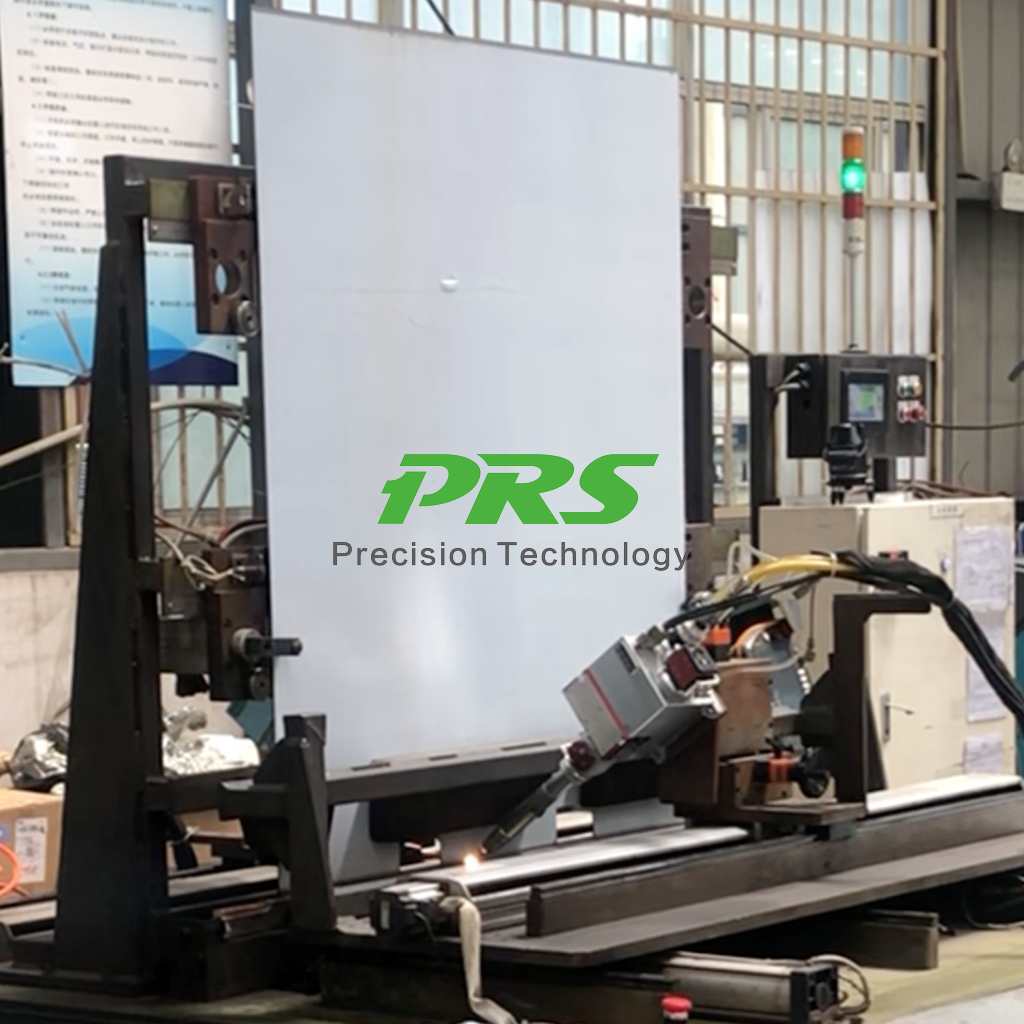
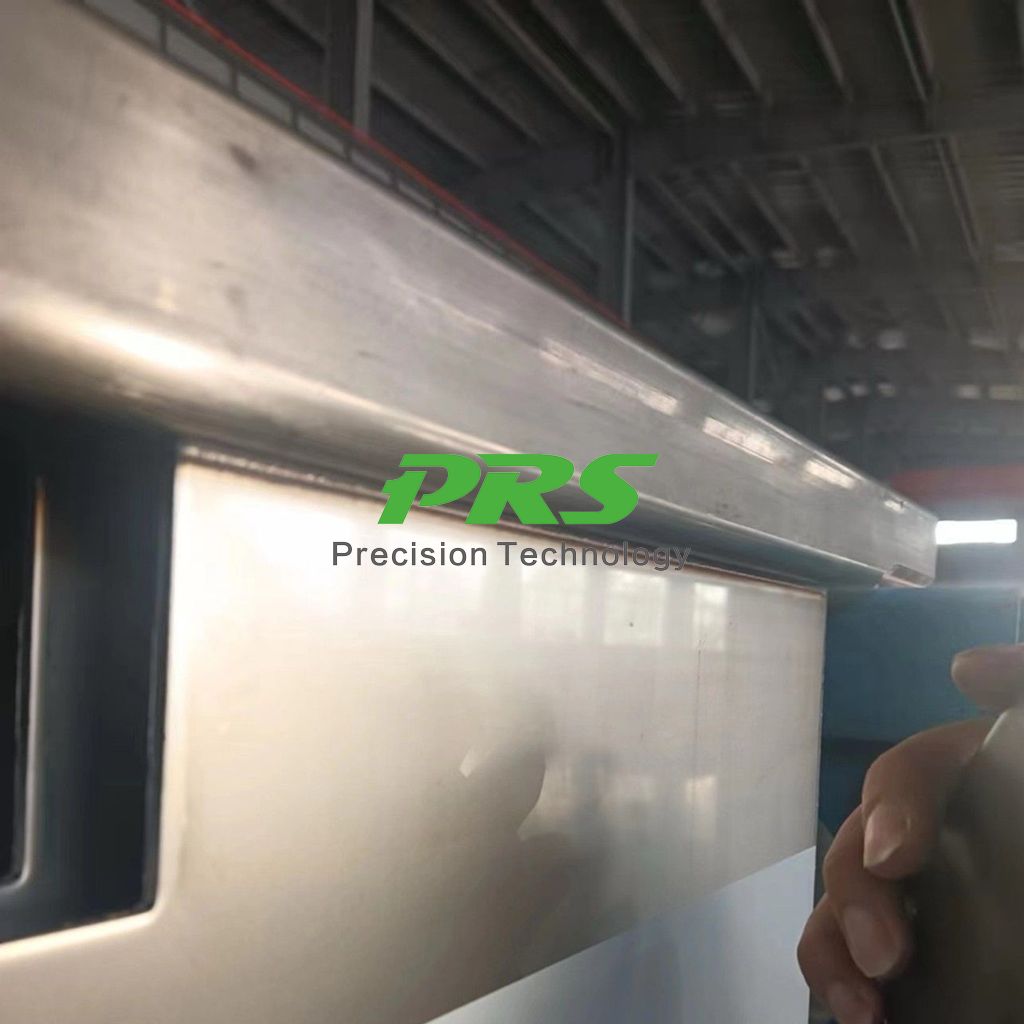
Laser welding of stainless steel plate
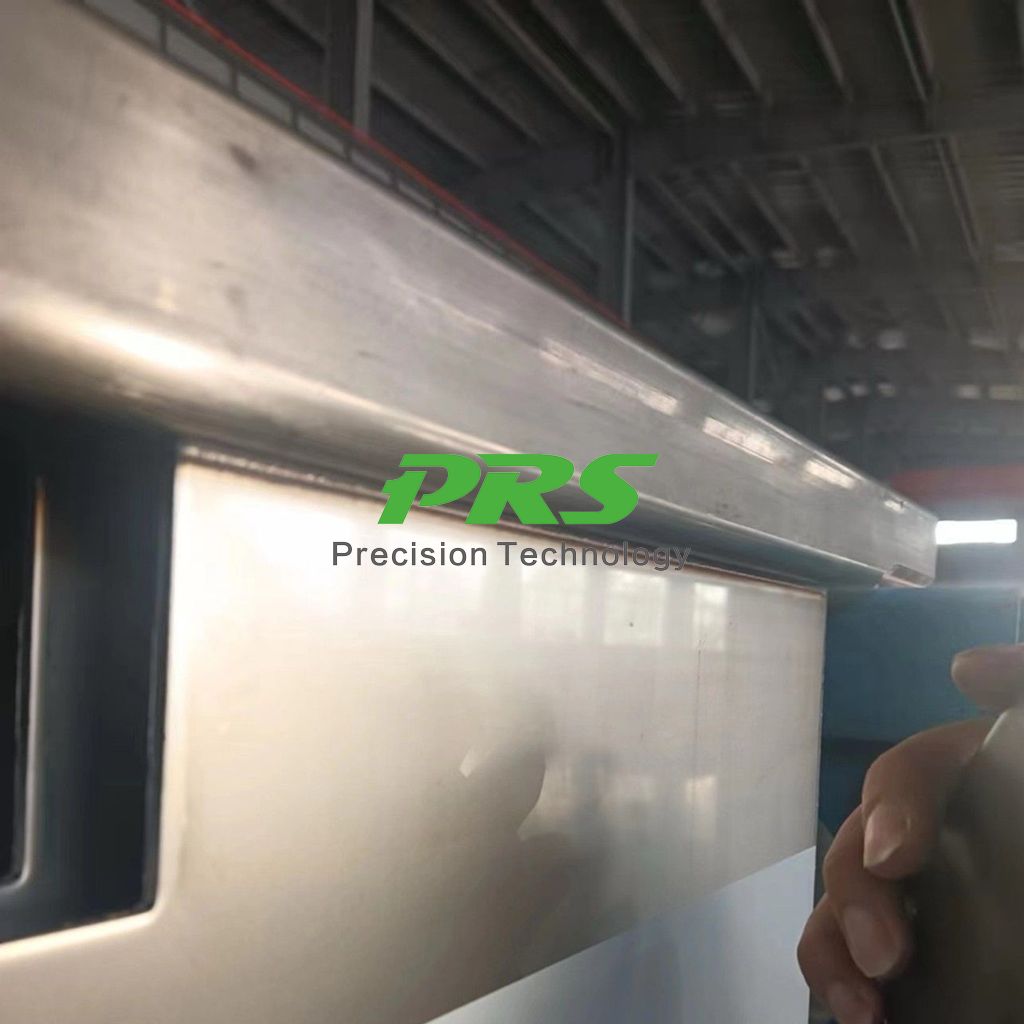
Laser welding of stainless steel plate
We use automatic laser welding as main method of welding stainless steel cathode plate. The pictures are as follows.
These images illustrate the precision of the welding area. In contrast to MIG welding, laser welding is more environmentally sustainable and safer for workers as it does not generate visible smoke or blinding light.
Optimal Welding Speed and Depth
we tested different welding speed and welding depth of automatic laser welding and find optimal welding speed and welding depth as show below.
Thus, our cathode, under normal working conditions, can last 15 years of service life. The Fig. 2 is the optimal welding speed and depth.
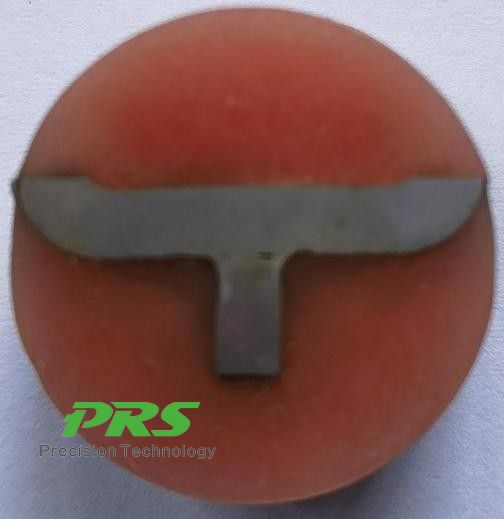
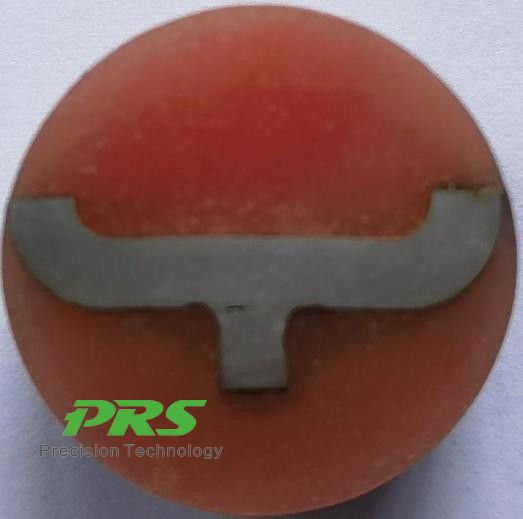
Fig. 1 sample one of our cathode welding cross-sections
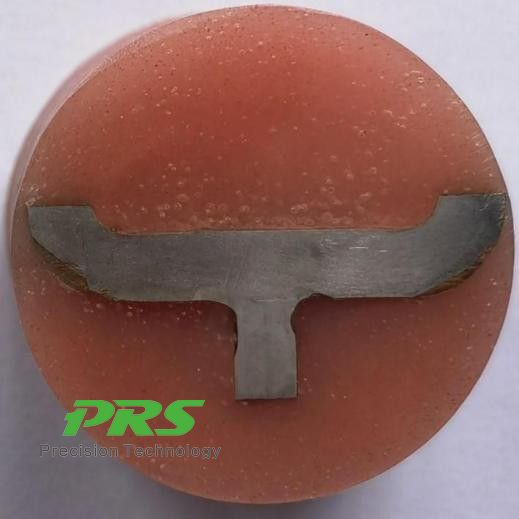
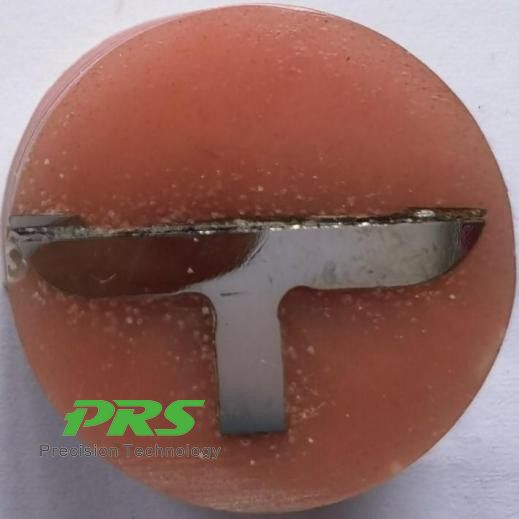
Fig. 2 sample two of our cathode welding cross-sections
We find the optimal welding speed and depth.
Conclusion
Considering the advantages of laser welding and the significant scale of this prospective order, it is advised to employ our automatic laser welding system. The automatic laser welding systemd can minimize energy consumption costs, enhance occupational health for workers, and more importantly guarantee product quality.
For a detailed visual guide, check out our Youtube vedio: https://www.youtube.com/watch?v=vV-_TzCHVks .
Contact Us
The SS316 Cathode plate laser welding developed by Sichuan Precision Technology Co., Ltd. combine innovative design, superior materials, and stringent quality control to deliver unparalleled performance and durability. These anodes are meticulously engineered for long-term use in copper electrowinning, ensuring consistent, high-quality results.